Easy Setup, Even for Beginners
Small robots OVR can help reduce setup time because dimensional data, such as arm length, is already registered.
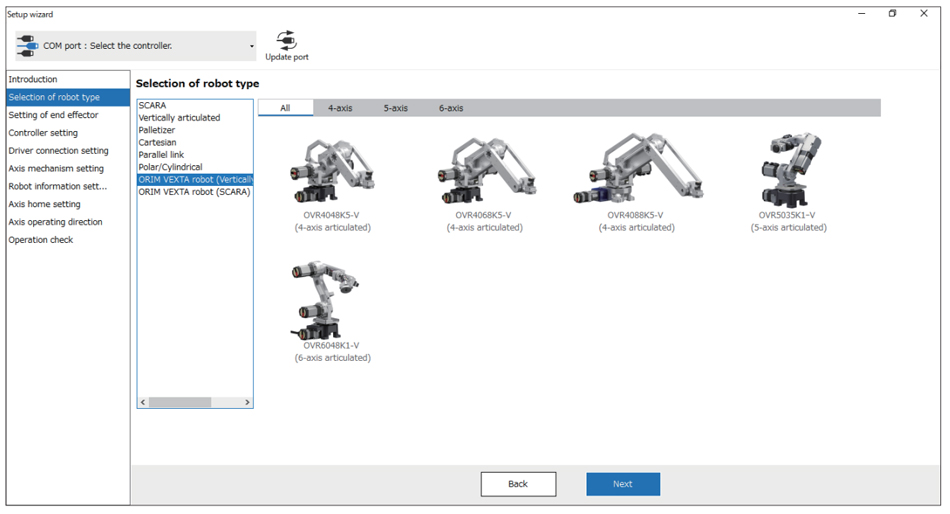
Say Goodbye to Ladder Logic! Operation Programming with Item Selection
Program creation uses a simple command selection format. Programs can be created intuitively, without requiring specialized knowledge such as ladder diagrams. The system supports a range of advanced motion control operations, including P-to-P, linear interpolation, circular interpolation, and arc motion, among others. Operating data is executed directly from a host controller via EtherNet/IP
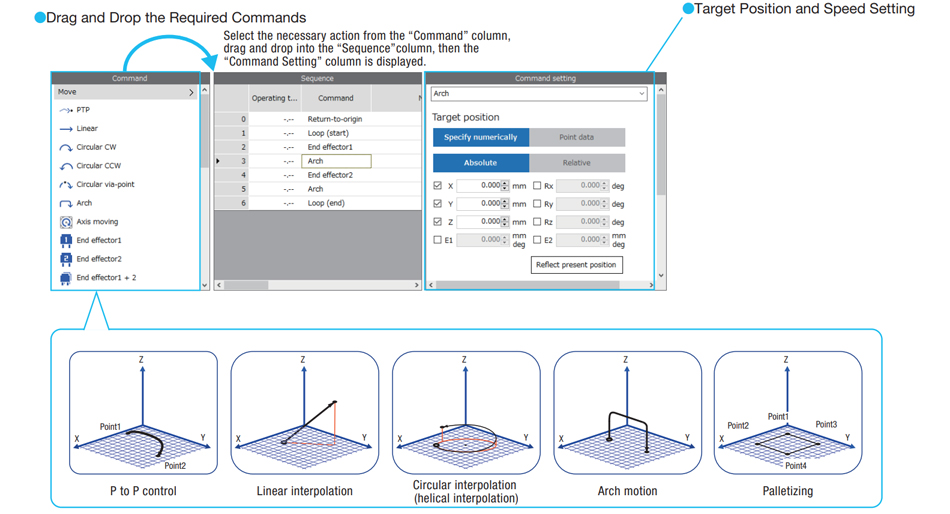
Configuration of a Robot Vision System Using 2D Cameras
The robot controller is equipped with useful functions for operating the robot using load position and angle information acquired by the camera.
In order to integrate the 2D camera, MRC Studio is used to perform the calibration* in advance. The settings can be easily confi gured by simply following the on-screen instructions while looking at the illustrations, allowing for a reduction in the work hours necessary for correction.
*Up to two motors
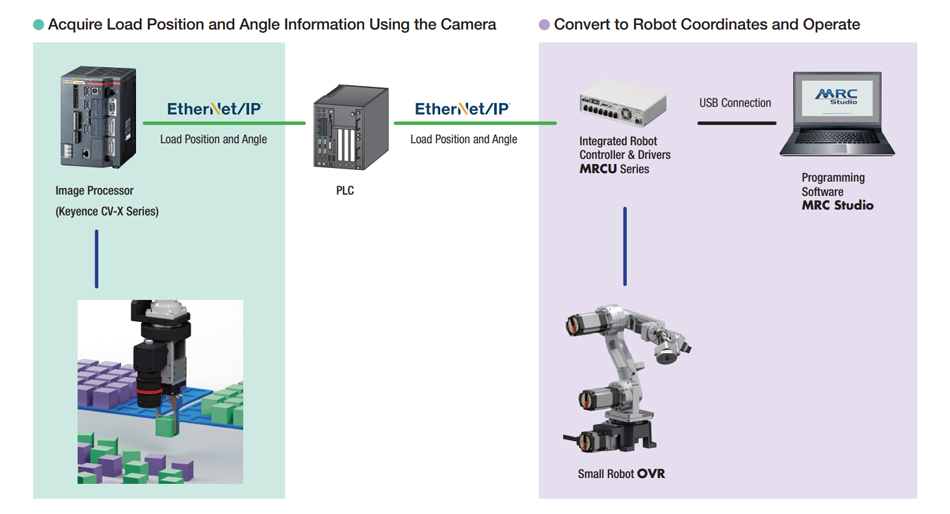