Oriental Motor offers industrial network communication products under the FLEX concept, meaning each product is equipped with an interface that connects to various industrial networks and master controllers featuring I/O; such as PLC, HMI or serial communication such as RS-485 / Modbus (RTU).
FLEX is the generic name for products that are used for Factory Automation (FA) network control via I/O control, Modbus (RTU) control, or a network converter. FLEX products enable easy connection, easy control, and reduce the complexity of system configuration.
Network Gateways for Factory Automation (FA) Networks
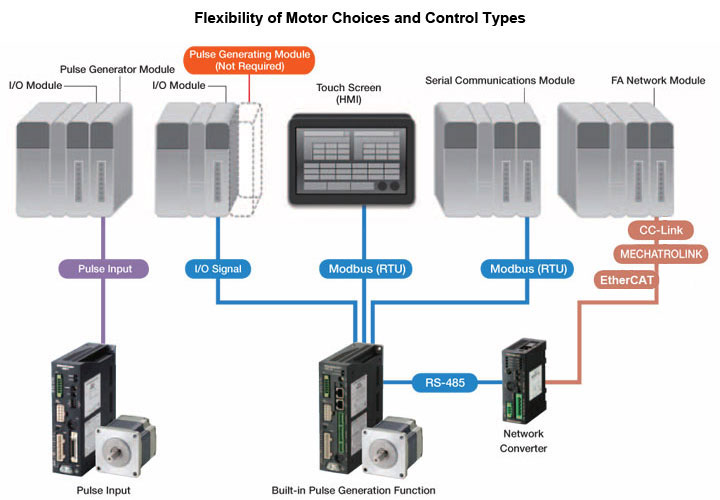
By using a network gateway, CC-link or MECHATROLINK communication are possible. Operating data, parameter settings or operation commands can be easily input.
CC-Link Control / MECHATROLINK Control / EtherCat Control
By using a network converter (sold separately), CC-link communication, MECHATROLINK communication and EtherCat communication are possible. Operating data, parameter settings or operation commands can be input via various types of communication. Since it can flexibly accommodate the networks specified by the end user, design time is shortened.
- The burden on the programmable master controller is reduced and costs are lowered when multiple axis are used.
- Compatible with various networks, allows for multiple axis or additional axis if needed.
- CC-Link compatibility: Max. 12 axis
- MECHATROLINK-II compatibility: Max. 16 axis
- MECHATROLINK-III compatibility: Max. 16 axis
- EtherCat compatibility: Max. 16 axis
- Can also handle group sending function between groups
Increased productivity is sought in manufacturing plants. At the same time, it is imperative to continue utilizing the knowledge of human experience through the use of Artifi cial Intelligence (AI). In order to use AI, it is important to collect, digitize and analyze the day to day “changes in conditions". Oriental Motor has created a wide lineup of products capable of outputting the various changes in conditions of motors.
In order to detect early signs of failure, it is important to monitor changes in operating conditions daily. One way to do this is to visualize position displacement due to fluctuation in temperature and operation time. This video demonstrates how the AZ Series works with an IoT setup to continuously monitor feedback information. Using this information, overall health of components can determined and manufacturing and productivity can be improved.